Linear actuators are of different types, and many ways to classify them exists. One of the simplest is to group them based on their drive mechanism. In that regard, the types:
- Screw-driven linear actuators
- Belt-driven linear actuators
- Motor-driven linear actuators
Which of the above should you use for your project? Well, it depends on the application. Each type has its pros and cons, and we’ll discuss them in detail below:
● Screw-driven Actuators
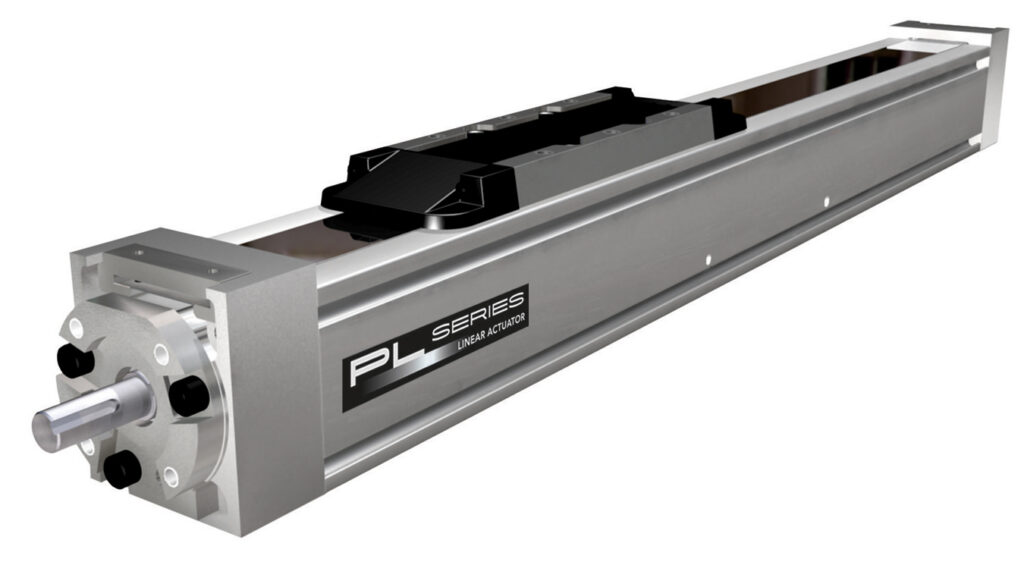
Source: amdc.org.mx
Screw-driven linear actuator components work using a screw and nut. They feature a rotating screw that converts rotary movements to linear movements. And they’re of different types, depending on the screw design.
You’ll find two main types of screw-driven actuators in the market. The first features an acme screw with a threaded rod. Such linear actuators can maintain a particular position for long without power. That’s thanks to their self-locking functionality.
The downside is that acme screw-driven linear actuators suffer higher friction. With high friction cones less efficiency and accuracy. If your task needs more precision, the second type, ball screw, will serve.
Ball screw drive linear actuators use a threaded rod, like their acme counterpart. The difference is that the threaded rod further includes a groove and ball bearings. As a result, they’re faster, with low friction and high accuracy. But there’s a downside: you’ll deal with loud noise.
● Belt-driven Actuators
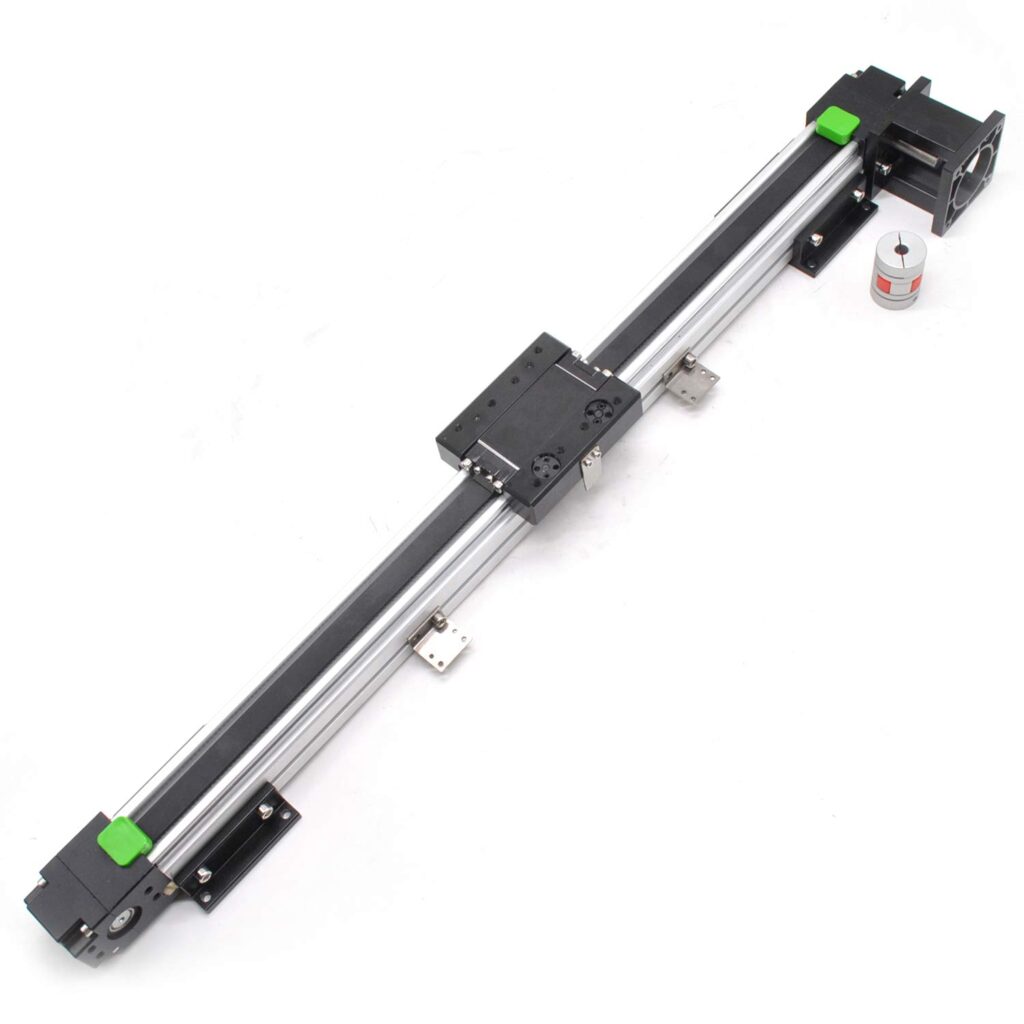
Source: amazon.co.uk
Belt-driven linear actuators function using a belt and pulley. The belt connects the control system motor to a carriage to generate linear motion. But how well the device functions depends on the belt type.
You can classify them by materials. In that case, a belt-driven actuator can feature a runner, steel, or plastic belt. But the more familiar way of organizing them is the belt design. You either go for a flat belt or a timing belt.
Generally, belt-driven actuators get appraised for high-speed and acceleration applications. They’re also affordable to buy and inexpensive to maintain. And thanks to their design, installation and mounting aren’t complex.
But belt-driven actuators fall short in a few aspects. They’re not too dependable for applications that demand high repeatability. Also, the belt — if rubber or plastic — can overstretch and cause a slip. Overstretching can occur when you overwork the actuator or if it encounters harmful external elements.
● Linear Motor Actuators
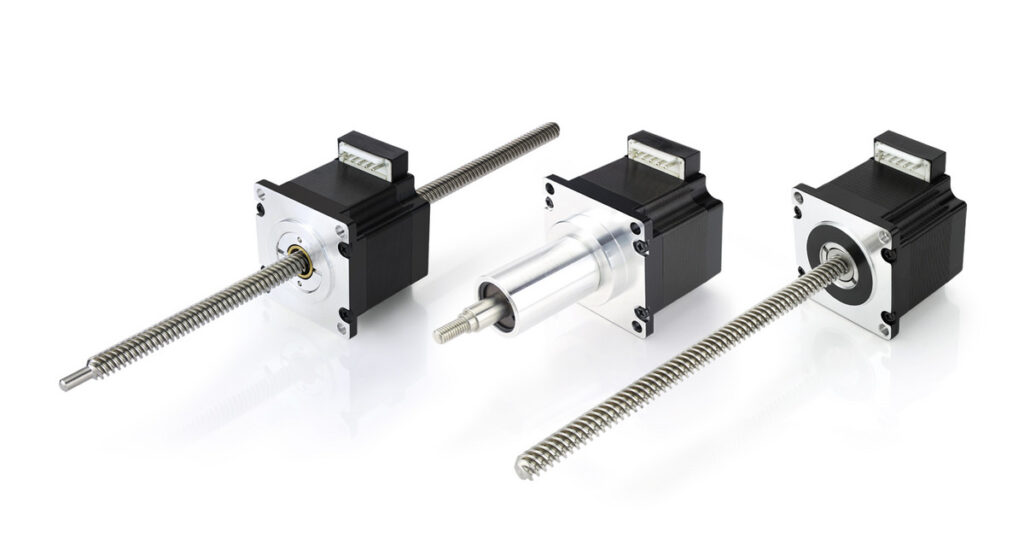
Source: en.nanotec.com
Linear motors are a constant in electrical linear actuators. They depend on electrical power to drive the actuator’s control system. Belts and pulleys and screws and nuts are out of the equation. As a result, linear motors don’t make much noise when running.
You can count on linear motors for more dynamic tasks that demand high accuracy and repeatability. For this reason, these motion devices are widespread in manufacturing, robotics, and aerospace.
Due to their wide versatility, linear actuators with an electrical motor cost more. Also, using the actuator may increase power consumption and add to your bill.
Conclusion
Understanding the different linear actuator types is straightforward. Expect a screw and nut if it’s a screw-driven actuator. For belt-driven options, you’ll find a belt and pulley. Meanwhile, linear motors use electricity.
You can rely on the concise pros and cons discussed in this post. With the information, compare the actuators’ performance. Then, decide which drive mechanism is best for your project.