The automotive industry is constantly looking for ways to improve production efficiency and reduce costs. One such method gaining traction in the industry is the use of 7075 aluminum extrusions in vehicles.
This powerful material offers a range of benefits that can help automobile manufacturers create cars with high quality, durability, and performance. In this article, we will explore how 7075 aluminum extrusions can be used to unlock potentials within the automotive manufacturing sector and provide insights into their advantages over traditional materials.
Optimizing Production Processes with 7075 Aluminum Extrusions
Optimizing production processes with 7075 aluminum extrusions can help automotive manufacturers to maximize their efficiency and create cost-effective, high-quality products. This type of metal is light yet strong, making it an ideal choice for creating durable parts and components.
Thanks to its superior heat conductivity properties, 7075 aluminum extrusions enable manufacturers to streamline the cooling process while reducing the time spent on each component. Furthermore, this material offers excellent corrosion resistance and can be machined or formed into a variety of shapes according to specific requirements to deliver optimal performance when used in automotive manufacturing applications.
By using 7075 aluminum extrusions in their production processes, automakers can reduce costs while ensuring that they’re creating reliable products that meet customer expectations every time.
Exploring the Potential of 7075 Aluminum for Automotive Applications
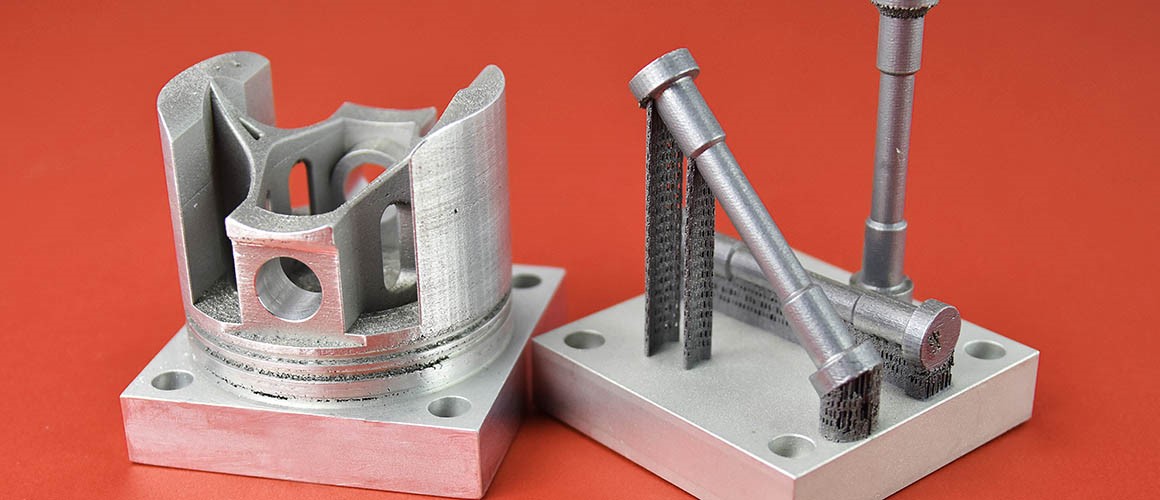
Source: .industrialheating.com
The automotive industry is continually looking for new materials to improve its products. 7075 aluminum extrusions offer immense potential in this regard, allowing manufacturers to create lighter and stronger components without sacrificing durability or performance.
With its unique properties, this material can be used in a variety of applications, from structural components such as frames to aesthetic ones like trim pieces. In addition to being lightweight and strong, 7075 aluminum extrusions are also very corrosion-resistant and have good thermal conductivity. This makes them ideal for use in both internal and external automotive parts due to their ability to withstand harsh environmental conditions while still providing superior strength-to-weight ratios.
Despite the clear benefits that come with using 7075 aluminum extrusions in the automotive industry, several challenges need to be addressed before it can reach its full potential. For example, it may require more specialized machining techniques than other metals due to its hardness which could lead to longer processing times and higher costs associated with production.
Moreover, any welding needs additional care since the heat generated during these processes could cause warping or embrittlement of the material if not done correctly. By exploring all of these different aspects when considering how best to utilize 7075 aluminum extrusion however, manufacturers can unlock tremendous opportunities for innovation within their products by taking advantage of its excellent physical characteristics while minimizing any associated risks or difficulties involved with manufacturing processes involving this metal type.
With some thoughtful consideration regarding deployment strategies along with appropriate planning around cost management strategies related specifically toward utilizing this unique material type – automakers will be able to find creative ways of incorporating it into various areas throughout their product designs – ultimately leading towards improved overall performance at lower prices compared traditional manufacturing methods!
Cost-Effective Solutions Utilizing 7075 Aluminum Extrusions in Automotive Manufacturing
The automotive industry is increasingly looking to 7075 aluminum extrusions as a cost-effective solution for manufacturing. With its high strength and durability, it has become a popular choice among manufacturers due to its ability to reduce costs while also providing superior performance. One of the main advantages of using 7075 aluminum extrusions in automotive manufacturing is that they are lighter than traditional materials such as steel or iron, making them ideal for applications where weight savings are important. This can result in improved fuel efficiency and lower emissions over time.
Additionally, these extrusions require less energy during fabrication, which can lead to reduced production costs when compared with other materials. 7075 aluminum extrusions offer excellent corrosion resistance too, which makes them suitable for use in areas vulnerable to environmental elements such as saltwater and humidity. Furthermore, their unique combination of good formability and machinability allows manufacturers greater flexibility when designing parts that need more intricate shapes or sizes than would otherwise be possible with standard materials like steel or iron.
Overall, utilizing 7075 aluminum extrusions in automotive manufacturing provides an attractive option for companies looking to reduce costs without sacrificing quality or performance standards. Not only do they provide significant weight savings but they also possess enhanced corrosion protection and machine-friendly properties that make it easier than ever before to produce complex designs quickly and efficiently at a reasonable price point – giving businesses the competitive edge they need in today’s challenging economic landscape.
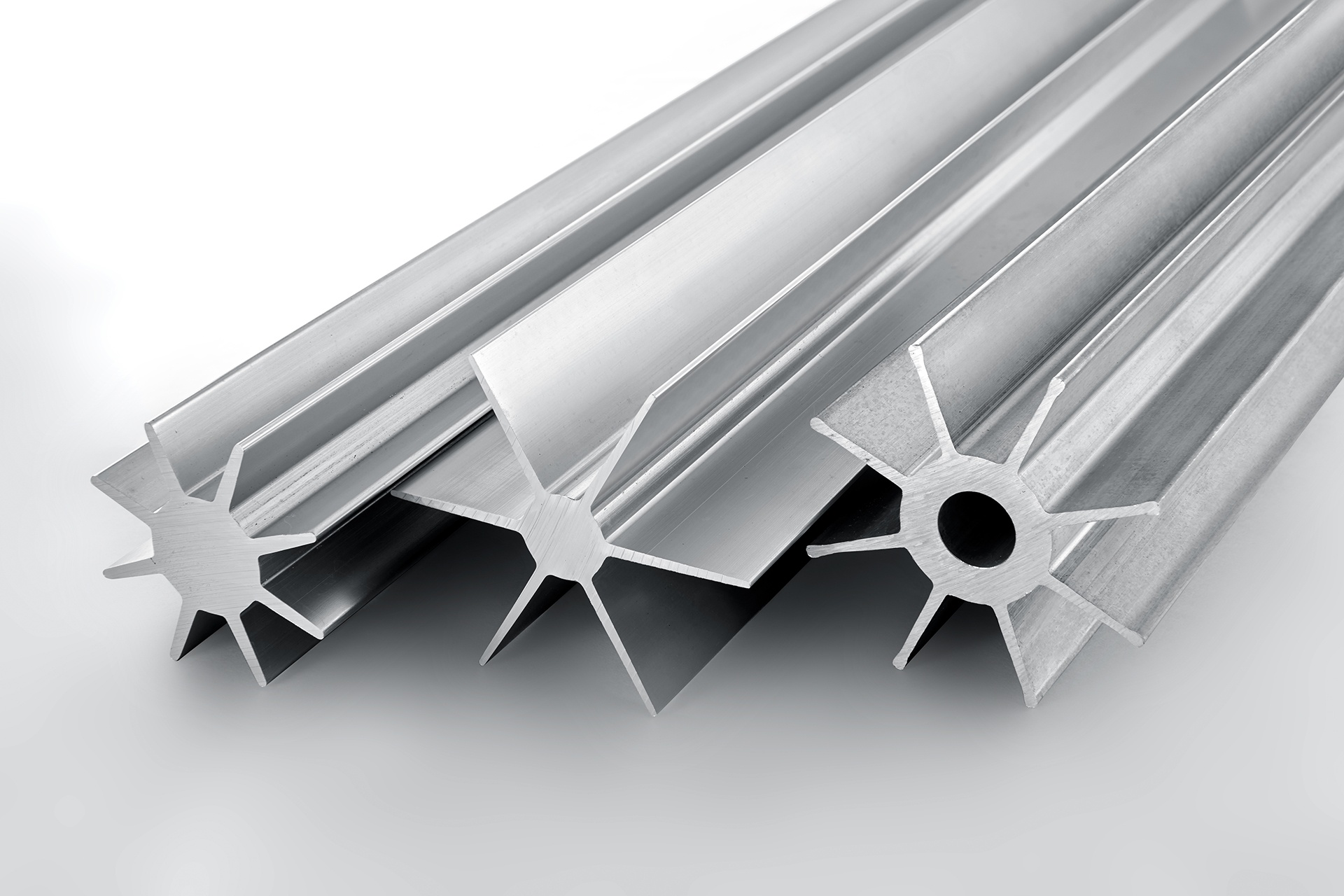
Source: pmcaonline.org